Introduction
Gouverner, c’est prévoir ; c’est aussi planifier. Bien que les concepts de base de la planification de la production se soient relativement stabilisés depuis une vingtaine d’années, il reste un long chemin à parcourir pour déployer ces processus au niveau optimal. En effet, les boucles de planification se révèlent de plus en plus complexes dans un contexte à forte pression concurrentielle et où la demande se caractérise par une volatilité et une instabilité croissante.
À cela s’ajoute des difficultés liées à l’environnement de production propre à certaines industries telles que l’industrie automobile, l’industrie aéronautique ou l’industrie maritime, qui présentent une forte variabilité des processus et des produits, ainsi qu’un nombre important de critères à respecter tels que le niveau d’encours de production, la capacité et la disponibilité des équipements, la priorité des lots, etc.
Face à ce constat, l’élaboration d’un plan de production optimal et réaliste peut sembler une gageure. Chez Planilog, il nous semble essentiel de porter notre attention sur l’un des niveaux les plus critiques de la planification de la production, à savoir : la planification de la capacité.
Qu’est-ce que la planification de la production ?
La planification de la production est un processus de prise de décision qui vise à prévoir l’utilisation des ressources et l’exécution des activités pour atteindre des objectifs déterminés.
Les ressources peuvent être matérielles telles que les machines ou la matière première, ou humaines, c’est-à-dire le personnel du centre de travail. Les activités peuvent être des opérations dans l’atelier ou des tâches (de maintenance ou de process) à effectuer. Chaque activité peut avoir un niveau de priorité́, une date de début au plus tôt et une date d’échéance de livraison.
Les objectifs d’optimisation sont nombreux tels que la réduction du temps de cycle, la réduction des retards, l’optimisation du taux d’utilisation des ressources, … Le processus de planification prend en considération le contexte et les contraintes internes et externes connues actuellement ou prévisibles dans le futur.
Les 3 horizons de planification de la production
Planification stratégique (long terme, 1 à 5 ans)
- Recherche de partenaires industriels
- Sélection de fournisseurs et sous-traitants
- Ouverture, fermeture ou délocalisation du site de production
- Lancement d’une nouvelle gamme de production
- Configuration de l’usine
Planification tactique (moyen terme, 3 à 6 mois)
- Plan Industriel et Commercial
- Plan Directeur de Production
- Plan de charge des ressources
Planification opérationnelle (court terme, 1 à 6 semaines)
- Ordonnancement des activités
- Pilotage et suivi des ateliers de production
- Gestion des règles de répartition de charge
Qu’est-ce que planification de la capacité ?
La planification de la capacité de production constitue le lien direct entre la planification stratégique et la planification opérationnelle (voir le schéma ci-dessous). Ce processus va permettre d’établir une liste de directives pour la production détaillée et la planification opérationnelle, soit la gestion du fonctionnement quotidien des ateliers de fabrication. La criticité de cette étape réside en ce qu’elle conditionne l’alignement de l’ordonnancement avec les différents horizons de planification.
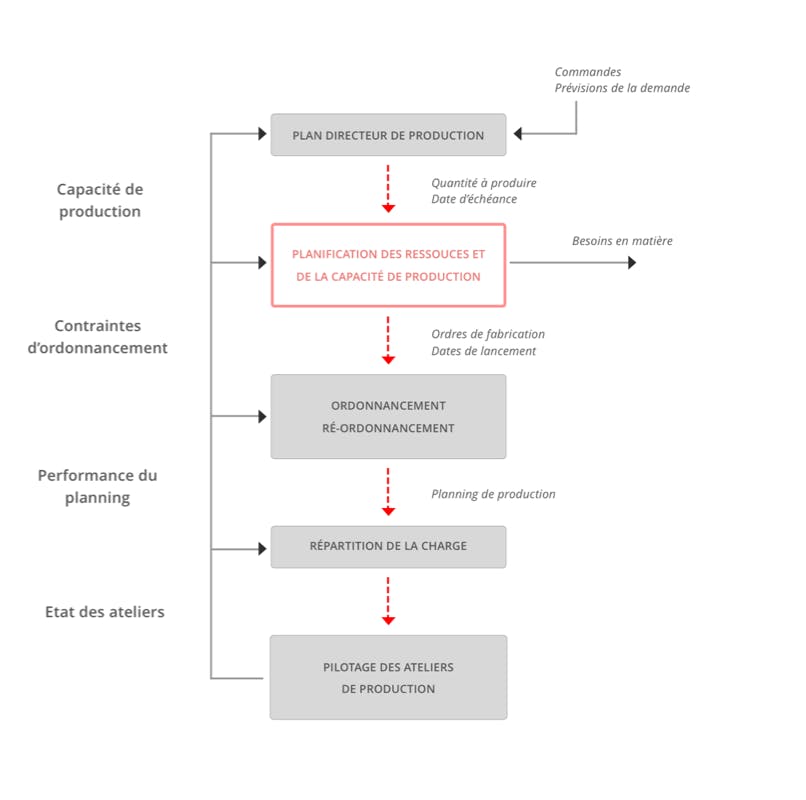
Par ailleurs, sa position centrale dans le processus de planification met en avant la possible divergence entre différents objectifs d’optimisation. Parmi les objectifs « classiques » de la planification de la production, on peut citer :
- L’identification précoce des goulots d’étranglement
- La satisfaction des livraisons clients (On Time Delivery – OTD)
- La réduction des encours de production (Work In Progress – WIP)
- La réduction des temps de cycle
- Le taux d’utilisation maximale des ressources.
Cependant, ces objectifs peuvent être contradictoire : en effet, la satisfaction des délais de livraison peut être inconciliable avec la réduction des stocks ou le respect des contraintes de capacité́.
Le but de la planification de la capacité́ est alors de trouver un équilibre profitable entre ces différents objectifs. Il s’agit d’établir un planning de production réalisable respectant de façon simultanée les capacités disponibles et les dates d’échéance de livraison en utilisant les équipements au plus près de leur charge maximale. L’action coordonnée est donc le facteur clé de réussite dans l’optimisation des flux de production.
Trois questions pour le planificateur
- Planification des capacités :
Quelle est la capacité nécessaire pour répondre à la demande ? - Planification de la production :
Quel est le plan de production le plus proche de la réalité en intégrant la demande et la capacité actuelle ? - Planification des encours de production :
Quelle est l’activité nécessaire pour assurer la livraison des encours de production ?
Les systèmes APS
Les systèmes APS ou Advanced Planning & Scheduling sont des outils d’aide à la décision pour une optimisation de la planification de la production sur différents horizons temps.
Ils sont considérés comme des extensions des systèmes ERP et GPAO qui sont dans l’incapacité de résoudre la totalité des problèmes de planification d’une Supply Chain.
Ils utilisent des méthodes de recherche opérationnelle et de mathématiques industrielles qui prennent en compte les contraintes de production et visent à l’optimisation de la Supply Chain en intégrant les objectifs de performance d’un ou plusieurs sites de production.
Notre solution Planilog
Étape #1. De la capacité Infinie à la capacité finie
Commencez par une planification en capacité infinie pour vérifier que toutes les données sont correctes. Toutes les activités doivent être planifiées et les dates de livraison respectées. Après avoir mesuré l’écart de charge, et paramétré le lanceur APS (Advanced Planning & Scheduling) en mode Capacité Finie, Planilog vous offre la solution la plus réaliste à appliquer.
Étape #2. Des contraintes non bloquantes aux contraintes bloquantes
Planifiez vos contraintes de ressources humaines, approvisionnements, semi-finis, matrice de temps de préparation et autres contraintes en mode bloquant. Le lancement du moteur APS Planilog en mode contraintes bloquantes vous permettra d’établir le planning de production le plus réaliste à partir de vos contraintes qu’elles soient de temps, de capacité, de priorité des lots, d’enchaînement, de batching ou de setup.
Étape #3. Démarche collaborative et Kaïzen
Utilisez les fonctions collaboratives de Planilog pour communiquer entre services et faire remonter les difficultés pour les traiter en mode curatif et préventif dans une démarche d‘Amélioration Continue des Processus.
Étape #4. Indicateurs de performance
Évaluez la qualité de vos plannings en vous basant sur vos KPIs et mesurez l’écart entre la situation actuelle et vos objectifs. Les indicateurs vous permettent de mesurer de façon objective l’efficacité de votre dispositif et facilitent le dialogue entre les utilisateurs intervenants sur des horizons temps différents (opérationnelles, tactiques, stratégiques).