
LISI Aerospace in context
LISI is a French multinational group (10,923 employees, 43 production sites throughout the world) specialized in fixation components and systems for the automotive (LISI Automotive), medical (LISI Medical) and aeronautical (LIRI Aerospace) sectors.
LISO Aerospace has been active in the aeronautical industry sine 1950, with more than 300 customers in 30 countries. The company is estimated at more than 1.3 billion dollars. LISI designs, manufactures fixations, assembly and structural components for the industry’s biggest international actors. With components and sub-assemblies strong in technical substance, the company differentiates itself by its ability to innovate and maintain consistently elevated operational performance.
LISI Aerospace is capable of responding to every type of production need, from pre-project to design, manufacture and delilvery of primary components and sub-assemblies, all in a well-managed program.
Ever more reactive and closer to customers: a permanent challenge.
The standards and certifications required in the aeronautical sector are numerous. They guarantee the quality of products, compliance with delivery dates and security. The challenge, then, is to guarantee a maximum of security for airplanes, while also allowing for reductions in production costs.
This is the mindset required within the company, rooted within all members of the team and supported by methodologies such as LEAP (LISI Excellence Achievement Program, based on the Lean Management and Six Sigma philosophies), as well as by the relevant training programs available through the LISI Aerospace Knowledge Insititute (LKI) and by general guiding principles such as customer-centric and results-based attitudes.
On the manufacturing side, the improvement of customer service is one important challenge in terms of growing customer satisfaction while optimizing performance in the supply chain.
Planilog’s algorithms
The ERP issues execution and production orders every week on an infinite capacity basis, after calculating needs. With Planilog, LISI Aerospace has access to a specific tool for optimizing rescheduling on a finite capacity bases for a horizon of three weeks. Each Production Order (PO) represents between 50 and 100 tasks. The objective is to eliminate bottlenecks while taking priorities into account.
Planilog APS increases throughput by using an algorithm that optimizes the scheduling plan while taking into account the known constraints specific to each machine, to each resource and to every customer need. Today, the three production entities use Planilog to process 70,000 POs. The optimization of flow scheduling has brought immediate results, such as On Time Delivery (OTD) that has progressed from 60% to 90%, not to mention better PO management. The success of this project was ensured through the participation and investment of production site leaders. Planilog offered an interative implementation mode that had the advantage of being rapidly operational. LISI Aerospace was thus able to get ahead of the progressive rollout new processes and the tools supporting those processes.
The project’s success is in the convergence of two factors, one human and one technical: the know-how of the Planilog team and their algorithms.
Ready to get started?
Start your free trial today or contact us if you have any questions.
Stay up to date with the latest information
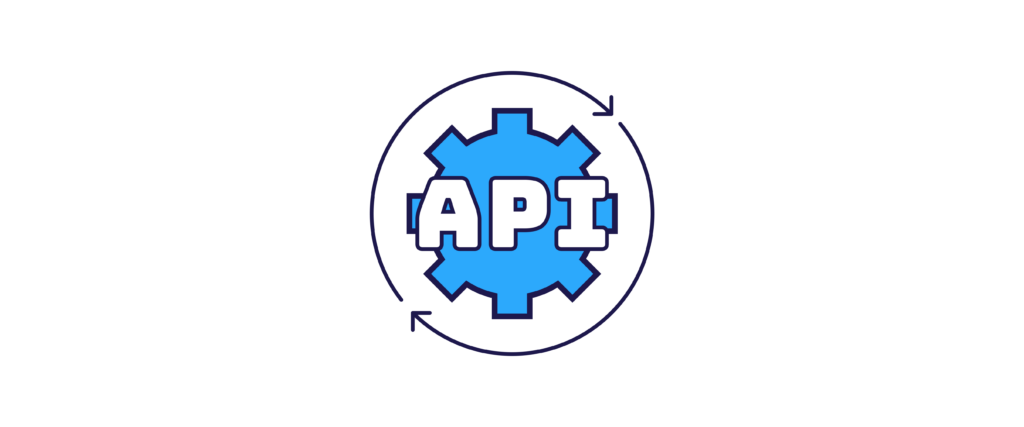
Simplifiez la gestion de vos données avec les API PLANILOG
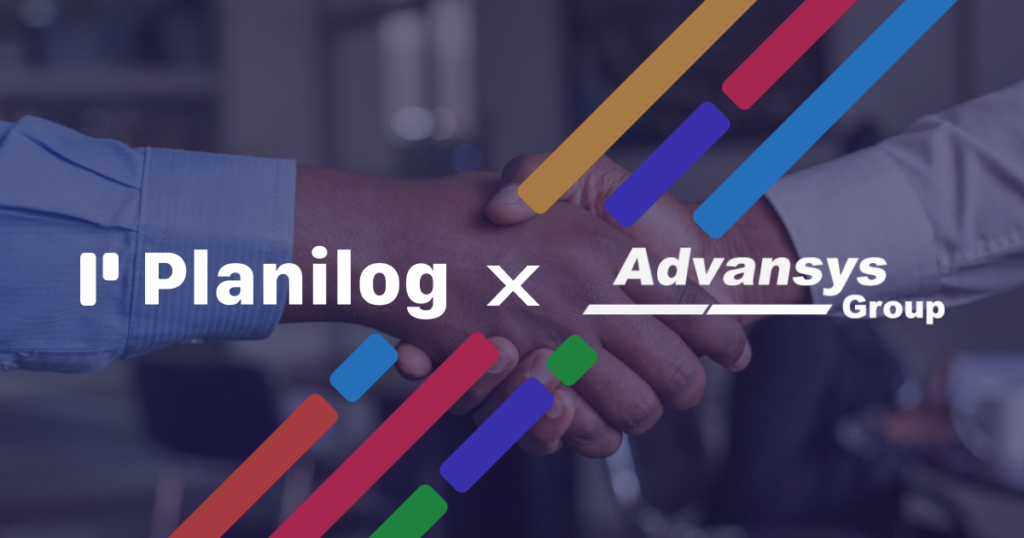
Nouveau partenaire : ADVANSYS Group, spécialiste manufacturing distribuera Planilog au Maroc !
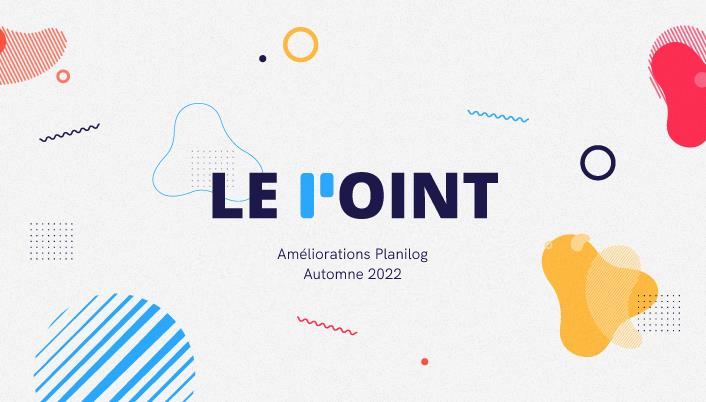
Les améliorations fonctionnelles de Planilog - automne 2022
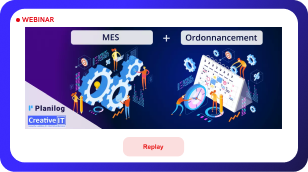
Une solution packagée MES + Ordo
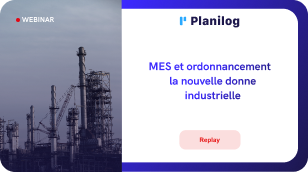
MES + Ordonnancement : la nouvelle donne pour gérer, planifier, suivre et mesurer efficacement !
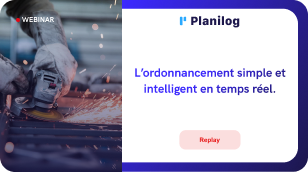
L’ordonnancement simple et intelligent en temps réel
Témoignage Nicolas Renard - La Manufacture Urbaine (S.E.M.U.)
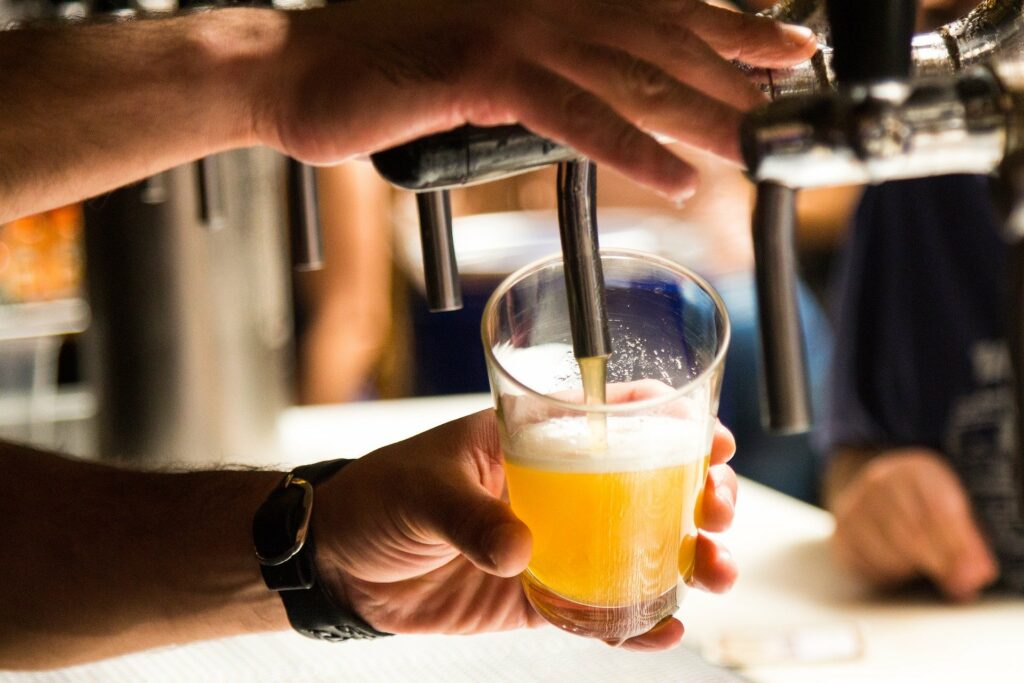
La Manufacture Urbaine (S.E.M.U.)
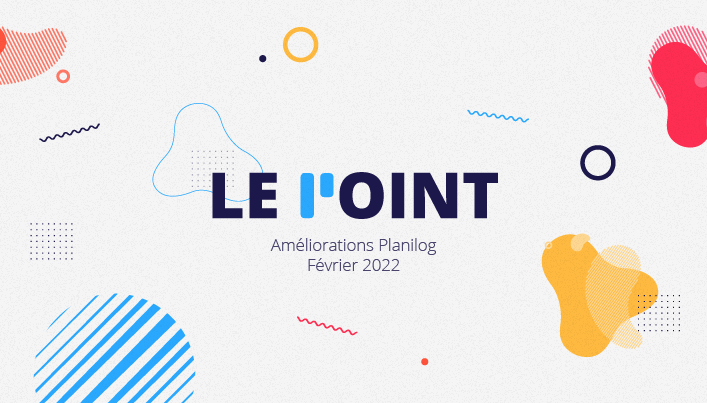
Les améliorations fonctionnelles de Planilog en cette rentrée 2022
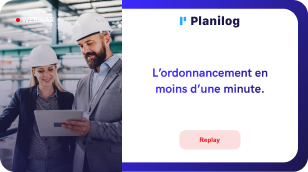
Ordonnancer de façon optimale en moins d'une minute, c'est maintenant possible !
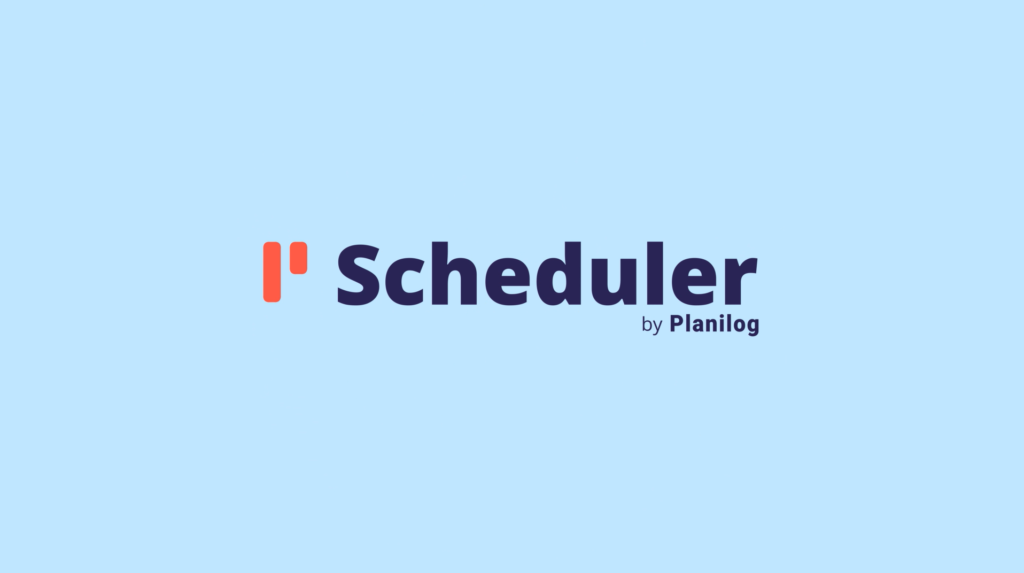
Planilog révolutionne l'ordonnancement avec le Scheduler
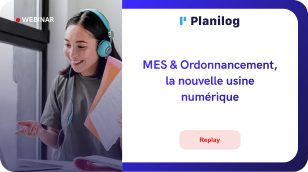